Modular, Incremental Production Capacity
Our pre-engineered production platform is created using Design For Manufacture and Assembly (DFMA) methodology. DFMA facilitates execution of multiple, manageable expansion projects in parallel, making incremental capacity available as needed. Modularized Extiel plants are optimized to leverage centralized US Gulf Coast fabrication capabilities to cost-effectively deploy production capacity in as little as 12-months.
DFMA also means production can be deployed almost anywhere: near the source of low cost pipeline gas or stranded gas; near the end user (even on the fence line) to minimize transportation costs and limit risk of supply interruption; within tax advantaged governmental jurisdictions; adjacent to synergistic process technologies i.e. refining, biofuel production and fertilizer manufacture, for example.
XTLG-500© Plants
Extiel GPG, LLC, a partnership between Extiel Holdings and Gulf Process Gases, produces the XTLG-500©, a fully integrated production platform that catalytically converts low cost natural gas into 500 Barrels Per Day (BPD) (23,000 MTPY) of high quality fully synthesized products. The unit is compact, modular and scalable for easy field deployment. In as little as 12 months, Extiel can deploy production capacity to explicitly meet supply chain demand.
The XTLG-500© is delivered as a complete package encompassing front-end feed gas compression through product storage tanks. Also included are Outside Battery Limit (OSBL) items normally left to the others, such as water treatment, cooling water system, control room, motor control center, plant air and nitrogen supply. The result is a tightly integrated, modularized, process package designed to reduce capital cost and improve operability. All of the process equipment is shop-fabricated in shippable modules that are deployable anywhere in the world, fully supporting Extiel’s distributed manufacturing model.
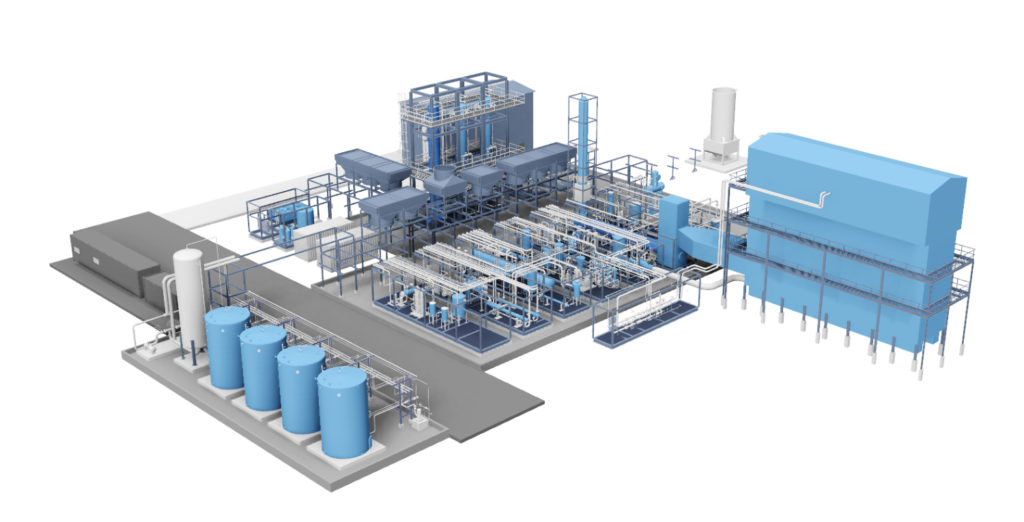
XTL-2000© Plants
The XTL-2000© is our larger production platform capable of producing 2000 BPD (93,000 MTPY) of synthesized product and can be deployed in as little as 18 months. Like the XTLG-500©, the XTL-2000© is a fully engineered package. The modular/scalable design approach maximizes shop labor and minimizes field labor allowing for low cost installation, even in less-than-hospitable or infrastructure-poor regions. The larger scale of the XTL-2000© offers greater capital efficiencies, significant improvement in operational economics and even lower CO2 emissions per unit of output.
For larger production requirements, Extiel has identified several plant sites capable of supporting ten or more XTL-2000© process trains. These sites offer excellent logistics, accessible property, ample labor force, abundant water supply and low-cost natural gas. A staged construction approach allows for near-term product delivery without the traditionally long project schedules associated with large capital projects.
Reliable Plant Performance
Extiel’s pre-engineered platform undergoes rigorous analysis for Reliability, Availability, and Maintainability (RAM). This RAM Analysis is conducted with world-class reliability experts who look at every piece of equipment in the context of overall plant function applying Monte Carlo Simulation methodology. The RAM Analysis informs operational and process design criteria in an iterative manner resulting in an optimized plant that balances capital cost, reliability, up-time and serviceability.
All of Extiel’s production is centrally monitored 24/7/365 by our team assuring operational excellence at all facilities. A myriad of data points is collected, trended and analyzed in real time, using predictive maintenance to deliver outstanding product quality and supply assurance. Centralized design, fabrication, operations oversight, services, continuous process improvement, product marketing, catalyst/consumables supply, production trend analysis, and predictive maintenance are under one roof to ensure stability of the distributed production model.
Product Quality Assurance / Quality Control
Product quality is important to our customers and is our top priority. Through a combination of operator training, documented operating procedures and integrated process control, Extiel’s Quality Assurance program assures the production of on-spec product. Under our Quality Control process, every shipment is certified by our on-site laboratory to meet strict specifications, assuring a consistently pure product supply.
Dedicated Supply Chain Partner
Make Extiel your dedicated, strategic supply chain partner. In as little as 12 months, Extiel can deploy incremental production capacity, to explicitly meet customer needs, providing a local source of high quality feedstock. Imagine distributed, line-of-sight production output that is synchronized with your supply requirements.
Our modularized plants are reliable, flexible and expandable to meet market demand at just the right capacity. Leveraging clean, abundant, low-cost natural gas feedstock, we synthesize high performance, paraffinic hydrocarbon chains in the C6 to C100 range. The synthesized solvents, base oils and waxes are unmatched in quality, performance and purity.